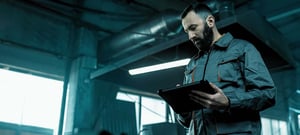
Plug & Play Machine Monitoring
Imagine being able to see every detail of your factory floor in real-time, from anywhere.
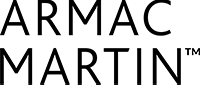
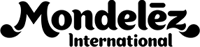
.png?width=200&name=MicrosoftTeams-image%20(130).png 1x, https://25959638.fs1.hubspotusercontent-eu1.net/hub/25959638/hubfs/MicrosoftTeams-image%20(130).png?width=300&name=MicrosoftTeams-image%20(130).png 1.5x)
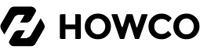
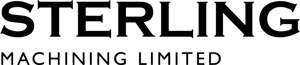

Introducing The MachineLink
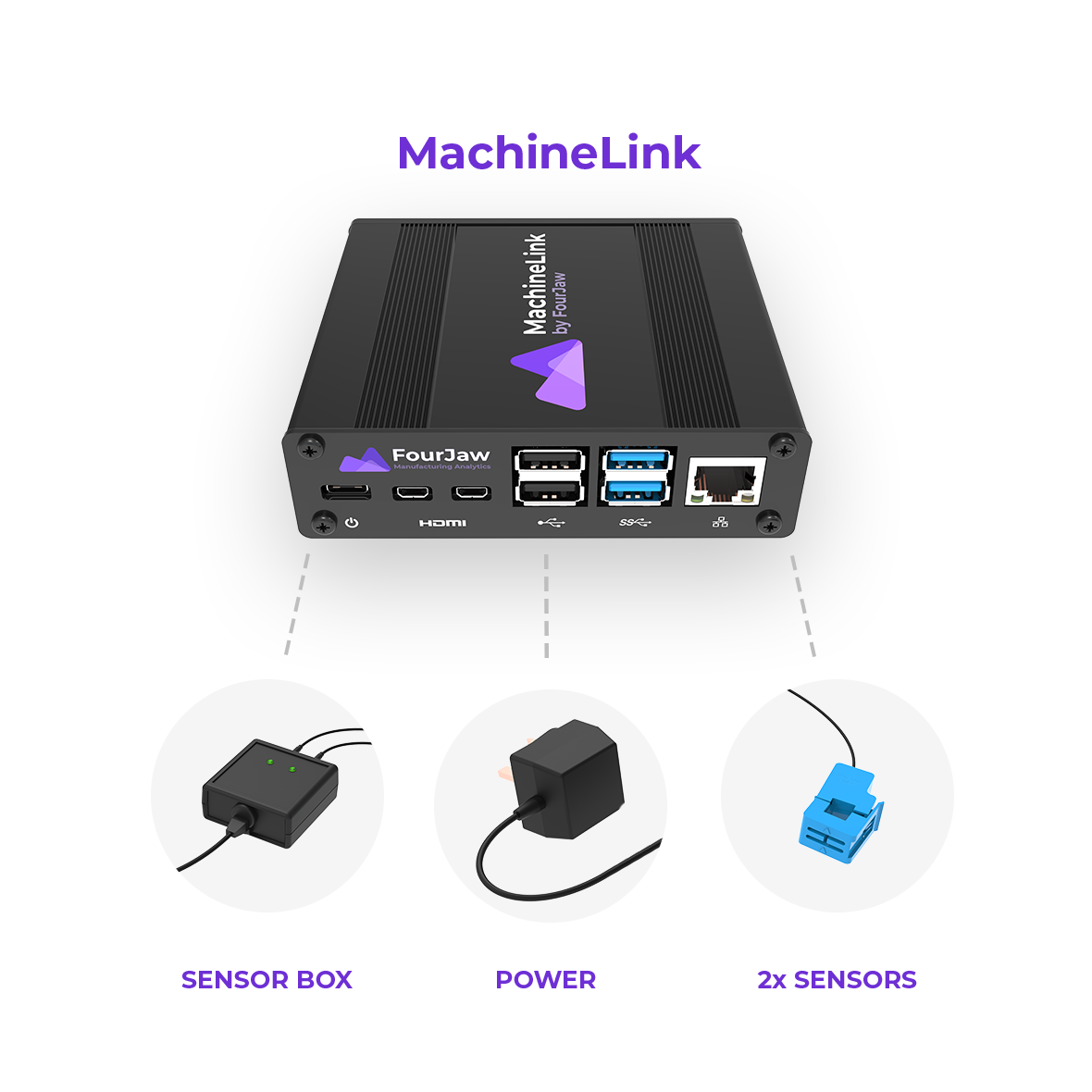
MachineLink uses simple current clamps and powerful algorithms to recognise when your machine is in a productive or unproductive state. It then sends this data to our cloud-based platform that you can access anywhere.
Install in as little as 10 minutes. Simply power the device, then clip the sensor to your machine's power cable, and data will begin to appear in your dashboard right away*.
As FourJaw is cloud-based, you can securely access your data anytime, anywhere. Security and feature updates to the platform are included for free in your subscription**.
The Operator Tablet
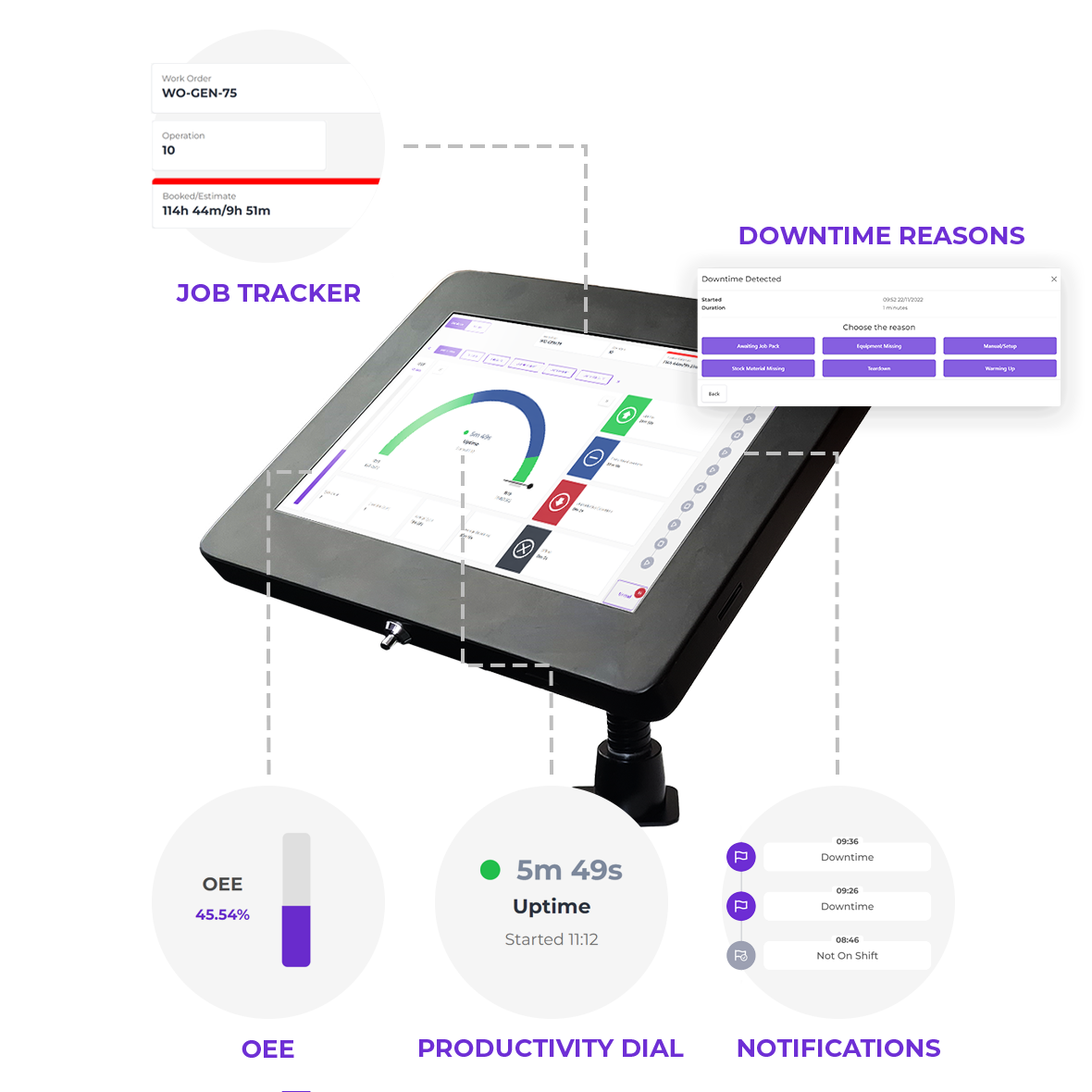
When MachineLink detects downtime, operators are prompted to select a downtime reason so you can use this information to drive productivity improvements.
Allow operators to job on and off from their machine to track time spent on jobs and schedule more efficiently.
The people who run your machines know more than anyone else about their machines. The tablet lets operators report production issues to managers so they can help operators be more efficient.
Turn Your Factory Into A Well-Oiled Machine.
FourJaw is specifically designed for manufacturers who are looking to do more with less, and find new efficiencies in their production process without wasting time or money on new equipment.
Plug & Play machine monitoring software is opening up a world of possibilities for manufacturers.
See the top downtime reasons by factory, cell or machine, to identify where the biggest productivity gains can be made and instantly take corrective action to make production improvements.
React quickly to production issues following event-triggered alerts. Escalate issues accordingly to remove bottlenecks before they cause disruption.
Stop The Guesswork
Reduce Production Downtime
See your biggest downtime causes so you can remove them. Benchmark productivity data over time to make sure utilisation is on an upward trend.
Understand & Improve OEE
Why did planned downtime take longer than expected? What was the quality of the output over the last shift? Get these answers and more....
No more wondering if "today was a good day or a bad day on the factory floor".
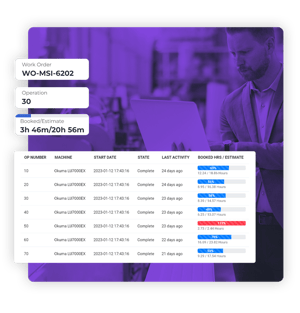
FourJaw Features
- Downtime Reasons
- Benchmarking
- Live Data
- Alerts
- Job Tracking
- Energy Monitoring
Downtime Reasons
Find out top reasons for machine downtime, by factory, cell, or machine. Take action where it matters most.
Benchmarking
Know your utilisation and OEE so you always know when things are going well (or not so well).
Live Data
See how your machines, lines, cells, or factories are doing without constantly patrolling the factory floor.
Alerts
With immediate notifications, factory managers can take quick action to prevent costly downtime.
Job Tracking
Keep track of jobs and analyse the efficiency that work-to lists are executed.
Energy Monitoring
See how energy usage translates to costs and carbon footprint to motivate change.
PLUG & PLAY ENERGY MONITORING
Unlike a standalone Energy Monitoring solutions, FourJaw combines Energy Usage Data and Machine (Productivity) Usage Data to drive sustainable, productive and profitable manufacturing.
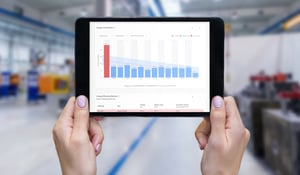
By machine, cell, production line or factory, in real-time and over time.
How FourJaw Compares
Move over traditional machine monitoring solutions. We’re on a mission to make access to machine monitoring as affordable and accessible as possible.
Get a Free Demo of FourJaw's Manufacturing Software
FourJaw helps you maximise productivity, optimise team collaboration, and make data-driven choices, all on one easy-to-use platform. Request a FREE one-to-one demo to unlock your factory's full potential today.
Measure
- Machine Utilisation
- Energy Monitoring
- OEE Monitoring
Analyse
- Downtime Reasons
- Job Tracking
- Custom Reports
React
- Live Data
- Chat Messenger
- Automatic Alerts
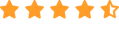
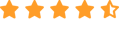
Frequently Asked Questions
Machine monitoring provides manufacturers with full factory floor visibility of how well machines are being utilised, by showing the machine downtime and uptimes.
With the FourJaw machine monitoring platform, operatives can categorise the reasons for the downtimes so factory floor managers get a clear picture of how productive the machines are. Here's a useful case study that shows how a manufacturer improved their machine utilisation by 400%.
No. Unlike traditional machine monitoring solutions, we designed our machine monitoring platform to be accessible, not only did we make it easy to install (minimising disruption to your shop floor) but we also made it affordable.
We offer monthly payment plans and you can install it yourself, so there are no high upfront installation costs often associated with traditional machine monitoring solutions. Find out more about the pricing plans we offer here.
Utilisation Data
FourJaw starts with utilisation data in it's simplest form. The specially designed MachineLink hardware is a combination of miniature computer and current clamps. These two current clamps are typically attached to the total power incomer of the machine and the main drive unit, for example a spindle motor of a CNC machine.
This raw data is recorded every second and sent to our secure Azure cloud platform. The data is then instantly built into chunks of running and not running data, typically over 20-second periods, which is then displayed and categorised throughout the FourJaw platform.
What this provides is a very accurate measure of when the productive part of the machine experiences load and when it does not. Applied to this data is FourJaw's Machine Learning program which automatically classifies the data into productive/active and idle/inactive time. This means warm up runs and free air cycles are classed as idle time in the case of a CNC machine as the machines is not in its productive state.
Downtime reasons are inputted by the operator of the machine via a tablet which is installed beside the operator.
Each tablet is paired with a machine via the same FourJaw portal running on a Chrome browser.
When the MachineLink hardware, detailed above, measures a set period of idle time a pop-up appears on the platform asking the user to log why the period of idle time has occurred, this can be inputted straight away, during the downtime or even post the downtime if required.
Yes it does.
Work order information can be inputted manually or directly imported from a .CSV file.
This data includes the WO number, operations, machine names, estimated job time and start dates.
As with all parts of the FourJaw platform, this data is combined with the downtime and utilisation data to provide meaningful and actionable insights into your production process.
As a manufacturer, it's highly likely you'll already be monitoring Work order times, Ops times and setup times, of course, this is all useful, however, it does not give you the big picture.
For instance, it doesn't identify and inform you of what improvements can be made to improve shop floor productivity.
Machine monitoring differs because it will give you real-time, actionable shop floor data such as:
- Top 5 downtimes, per factory, cell or machine
- Pareto plots
- Average setup time per part
- Downtimes and machine active times per work order
This information can be used to take decisions based on fact and not opinion.